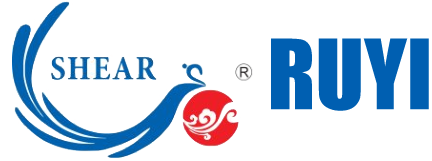
Adhere to the business philosophy of people-oriented, honesty and enterprise; assist customers to be competitive.
Source: Ruyi Transformer Equipments Manufacturer Co.,Ltd. Release time:2022-08-22 11:19:20 Author:3825
If the gap between the molds is too small, the upper and lower cracks cannot be connected, but are parallel to each other at a certain distance. When the material is best separated, due to extrusion, burrs, cracks or flakes will appear in the cross section between the two cracks, and the upper part of the workpiece will form a second glossy narrow with a burr or toothed edge strip, the narrow strip is inverted conical and easily gnawed on the die. The service life of the mold will be shortened.
To solve the burr problem, in addition to requiring the mold designer to correctly select the mold material, structure and clearance; the manufacturing personnel should strictly grasp the key points such as processing and fine grinding to make the finished mold qualified. In addition, the following requirements must be made to the operator:
1) Carefully install, repeatedly adjust and check the mold carefully, so that the mold is in a normal state from the beginning of use. Try to avoid a lot of waste caused by improper adjustment, and the mold will be disposed of after being gnawed.
2) After punching or cutting a small amount of finished products, insist on self-inspection and random inspection. If the burr exceeds the standard, take corresponding measures to solve it in time, and check regularly in the future.
3) When checking for burrs. Generally speaking, the burr height can be measured with a micrometer, or it can be touched by hand (do not touch when the machine is running). when
3. In contrast, measuring instruments or optical instruments can be used, which have very small edge deflection and arc deviation values, as well as microplatform silicon steel transverse shear lines. Obviously, the angular error and length measurements of the finished product are different due to the different methods used.
The above is the impact of the slitting and horizontal shearing on the quality of the iron core brought by Ruyi Technology. You are welcome to come to our company for the needs of the horizontal shearing machine!